Power Masters: Motorsports Driveline Components
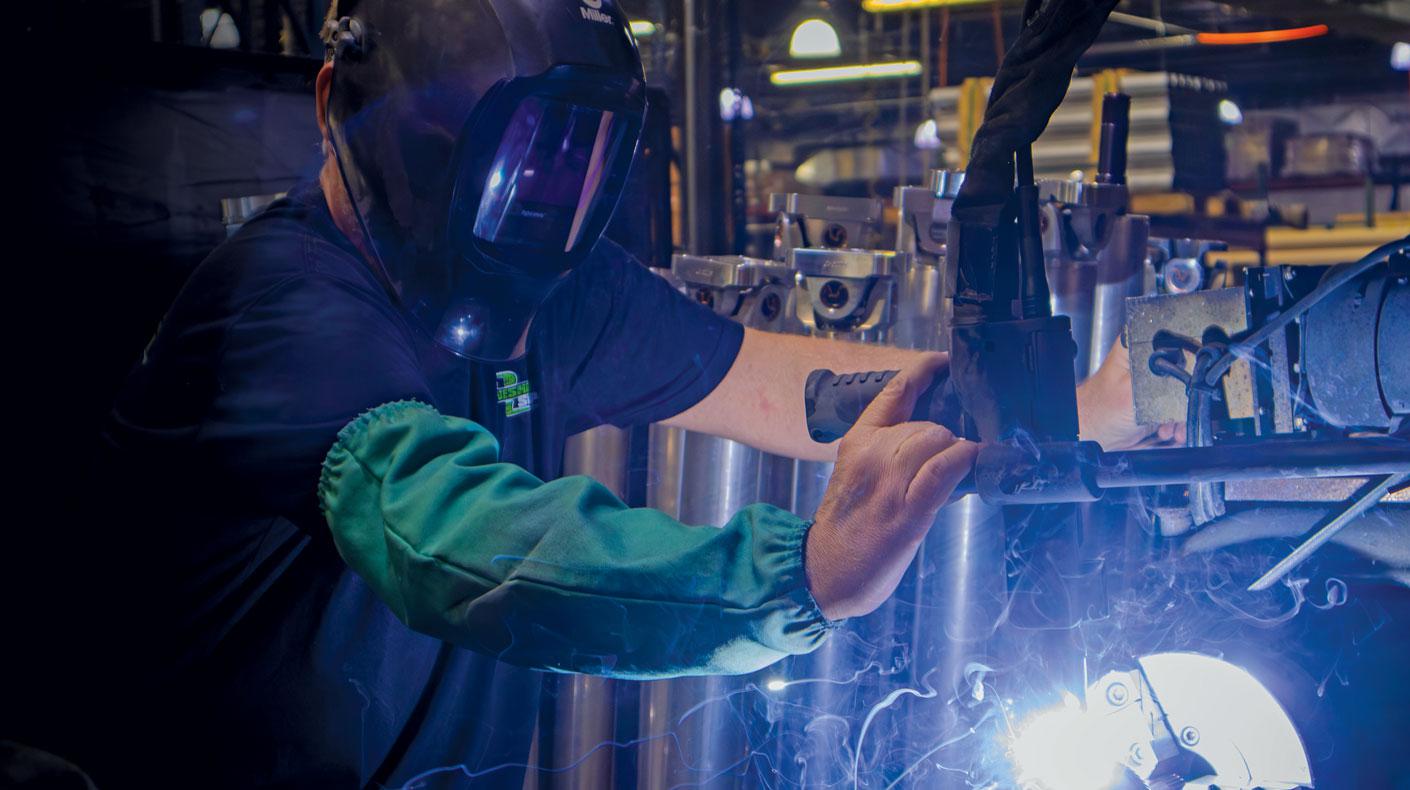
How today's race driveline components are designed and manufactured to endure ever-increasing levels of horsepower and torque.
The light flashes green, and in an instant, a shattering amount of pure kinetic energy slams through a vehicle's driveline. Failing to handle it could be disastrous to the point of a wreck. Harnessing it, amid ever-rising power levels for everything from race cars to hot street machines, is the mission of aftermarket firms that specialize in performance powertrain management.
Increasingly, these firms have their work cut out for them. There was a time when a street-legal vehicle making 1,000 horsepower was all but unthinkable. Now, advances in engine technology—particularly turbocharging, supercharging, and nitrous oxide systems—mean heavily modified street cars and light trucks routinely pound out 3,000 hp at the wheels, or more. The specialty firms that address this reality now rely on ultra-hardened components, evaluated with input from customers, that allow these outrageous outputs to be reached on the street, drag strip, and road courses.
One such firm, Quick Performance in Ames, Iowa, markets axle and driveline components from a number of prominent producers and uses them to come up with high-horsepower solutions for customers in a variety of competition disciplines.
"We've been here since 1987, and we've got quite a few different avenues for circle track, drag racing, and autocrossing pretty much every day," Ashton Thompson said. "We've also got pulling tractors, rock climbers, and hot rodders. We have our name on nearly everything from the guy with 400 hp going to a Friday test-and-tune night, right up to 3,000-hp drag cars."
Quick Performance sells driveline gear from some two-dozen suppliers, including Eaton, Spicer, and Strange. The inventory is backed up by inhouse work that provides a particular driveline for a specific customer's needs.
As Thompson explained, "When it gets to the real high-horsepower stuff, Strange Engineering is going to be our go-to for most of those applications. Strange has a really nice floater kit with 40-spline axles. It also has a really nice billet case, which is good, because distortion is the big problem with high horsepower. Here, we do chromoly housings, quarter-inch tubes, 3.5-inch axle tubes, 40 splines inhouse, gun-drilled axles plus either 31 or 35 splines, depending on the horsepower needs."
S&S Truck Parts of Crown Point, Indiana, supplies various driveline components. For severe-service use, Jeff Belknap said that S&S focuses on an extremely durable ring-and-pinion assembly sourced from its brands Motive Gear or Richmond Gear, depending on the intended use. Motive Gear components are mainly used in off-road and Trophy Truck-type vehicles, while almost all drag racing uses involve Richmond Gear parts.
"We have ring-and-pinion sets for 9-, 9.5-, and 10-inch for high horsepower, basically ranging from 750 hp all the way up to 5,000 hp, and even more," Belknap said. "When we get into a couple of thousand horsepower, you've got to go to the bigger 10-inch diameter, and you go from 8620-rated steel material to 9310, which allows the tooth to flex a little so it's not as brittle. The drag guys get 50 to 60 passes on a ring-and-pinion set, and what they don't like is a lot of heat for a long period of time, because these gears would eventually melt down. With 9310, and Rockwell heating 57 to 59 range [the level of heat applied], you really have to watch Rockwell heat in the process because if it gets too high, the gear gets brittle and would want to break. You get the forging of the gear, a Gleason machine cut with five passes, then heat-treatment."
Specialized Components
Circle D Specialties in Houston, Texas, is well known for its performance torque converters, which are applicable for anything from hot street cars to drag use with outputs up to 5,000 hp. "Torque converters are our primary product, with transmission casings secondary," said Chris Sehorn. "We have 252-mm and 264-mm converters that are good for 5,000 hp, up from 3,000. We use software to do a lot of testing, computational fluid dynamics for internal-flow performance, and finite element analysis to develop the structural integrity we need to make sure it can hold that kind of power."
Circle D's Ronnie Combs added that manufacturing considerations include material choice and heat-treating. "We design everything using finite element analysis with stiffness in mind, because flex is the major problem. We look at a good strength-to-weight ratio and stiffness. When you look at the natural progression of power output over the years, 3,000 or 4,000 hp isn't that crazy anymore, so what we do here is mainly going to be drag racing."
Another highly specialized part is produced by 6XD Sequential Gearbox in Kannapolis, North Carolina. An inhouse sequential transmission rated at up to 1,800 lb.-ft. of torque is the firm's main product. Clay Stephens said the transmission is aimed at street cars, drifters, and increasingly, competitors in the Trans Am classes such as TA1, where Amy Ruman and Kerry Hitt both use the gearbox.
"When we started building these in America, most of the sequentials offered in America were for foreign cars, so you couldn't find a bellhousing for them," Stephens said. "We use a standard Muncie bolt pattern at the front, so there's tons of bellhousings out there for them, since all NASCAR transmissions and drag racing use that bolt pattern. Our transmission shifts faster, and you can slam it into the next gear because of positive engagement, where the driver just has to pull the shift handle back to upshift. Our standard is around the 2,200-hp mark, but we have people in the Dodge Viper community running the Texas 2K and Florida 2K that have 2,000 hp to 4,000 hp in street-legal cars.
"What we do is very simple," Stephens explained. "The gears are larger, there's more bearing surface, and the bearings are bigger. We supply everything from the Vipers to some diesel, and we have a stronger gearbox for 3,000 hp. The transmission is longer because the casing is longer, with six forward speeds."
Hardened axles are the primary products from GForce Performance Engineering of Overland Park, Kansas. Many have CV joints and shafts, aimed at installation on modern domestic and imported performance cars with independent rear suspension. According to Jesse Powell, the firm's manufacturing philosophy is based on the fundamental understanding of vehicle physics between heavier street vehicles and all-out drag cars.
"One thing that's unique to us is that a lot of cars we deal with are 1,200- to 1,500-hp street cars. Is it the same as a 3,000-hp Pro Mod? The answer is 100%, and in some cases even more demanding," Powell explained. "We look at power-to-weight ratio. About 1,500 hp on a 5,000-pound street vehicle is a bigger demand on the driveline than a 3,000-hp vehicle that weighs 1,800 pounds. We focus mainly on IRS [independent rear suspension] later-model vehicles, which means the axles themselves; the halfshafts themselves. All new vehicles including BMW are now IRS, so performance vehicles are using halfshafts, even as the performance of these vehicles has just continued to climb. Twenty years ago, the first domestic vehicles with IRS made barely 300 hp. If it was 600, you were making a lot of power. Today, you can sneeze on these engines and make 1,000 hp."
Besides axle halfshafts, GForce also produces performance driveline bushings with premium metal cores that limit excess movement. "The rear cradle on a soft chassis bushing produces a comfortable ride," Powell said, "but once under load, those things start moving, things get out of alignment and you start breaking bolts, axles, and driveshafts. Our bushings hold all those things in place as power increases.
"Our bushings are polyurethane based," he continued. "Not just a puck poured into a mold, but also engineered with steel or aluminum sleeves or cores. Additionally, these bushings feature different durometer polyurethane within the bushing to give you a more pleasant driving experience, but more rigid control when under load. With the axles, you only have so much material that you can work with because it has to fit into the differential and into the hub. The spline count does not change. The only way to make it stronger is to use better materials."
Transmissions and torque converters for extreme service are also the primary products at FTI Performance in DeLand, Florida, part of the Wharton Automotive Group founded by Funny Car racer Paul Lee. Another nitro racer on the company's staff, Krista Baldwin, said, "We make many high-end horsepower components meant to survive the abuse you give it on your weekend exploits. One of our most popular is the Turbo 400 transmission, which is listed as up to 2,000-hp capability. We put an aftermarket SFI-approved case on it. Then we go into its internals. We switch out to aluminum drums and use billet planetaries. We improve the internal and external dump valves. We also have the customer fill out a comprehensive build sheet. We want to know everything possible about your build: vehicle weight, rear ratio, tire size, engine dyno numbers, fuel delivery, intake manifold information, cam specs, and whether you're using nitrous, a turbo, or supercharger. You spent so much money to create this power, so we have to build a transmission or converter suitable for that power and for your application."
If a car is making 3,000 hp on the street, "you're most likely going to take it to the race track," Baldwin continued. "If your vehicle has any track time, it results in changes that we do for your combination. When we go through the build sheet, we want to know where you're taking this car, on what kind of track surface. Obviously, the converter is meant to multiply the torque. You don't just want to blow the tires off when you step on the gas. That's why every converter is custom built, with billet steel stator components, reinforced steel bolt-together rings, everything CNC-machined, plus we can add a billet aluminum torque converter cover. All the internals are TIG welded."
Durability Tested
The DriveShaft Shop in Salisbury, North Carolina, has produced stress-hardened axles and driveshafts for more than 30 years. The components are made inhouse and then sent out for destructive testing. Lee Mejia noted the company is highly involved with numerous Formula Drift teams who "run our CV axles and carbon driveshafts. So do a lot of hill climb vehicles, including Pikes Peak. We also do lot of road race applications. A lot of it is custom builds, big-horsepower street cars or modern drivetrains in older vehicles. We apply knowledge from what we know works and create solutions to problems they're having on the street."
The DriveShaft Shop uses "300M material for all CV axle bars, aerospace grade materials, not just for strength but also durability over repeated shock loadings," Mejia said. "We do all splining inhouse and thera-coat [apply thermal coating] a lot of products inhouse. We have a full engineering department where we model our own parts. The big thing that sets us apart is our ability to see a part and create it from scratch, inhouse, to deal with a race application."
Advanced Clutch Technology (ACT) in Lancaster, California, specializes in torture-tested clutches, another component that can be hammered in high-horsepower scenarios. The firm works extensively with sponsored racers during its R&D process.
"Advanced Clutch Technology is unique because inhouse engineering makes up 15% of our workforce," said Rich Barsamian. "Our engineers design and develop our diaphragm springs and faces from scratch. This allows us to maximize the clamp load increase exponentially and minimize the increase of travel and pedal effort. We approach the specs for each application differently. Therefore, the different engineering enhancements will vary depending on the vehicle. ACT chooses Cerametallic six-puck or sintered-iron friction material for our clutch for big-power racing applications. We also have a test vehicle, for which engineering built a quick release for the bellhousing, allowing us to change friction discs in 15 minutes. To meet these high-horsepower engines, we are constantly testing new friction materials looking for the best of the best."
Dyno testing at ACT applies a controlled load to the clutch assembly to ensure a proper torque capacity. ACT clutches are then heat-treated to limit premature wear and failure. Dyno testing also allows engineers to run the clutch through repeated heat cycles to determine its durability. Engagement and release characteristics are critical for racers needing precise launch characteristics and shift performance. The dyno can also simulate either street or track performance loadings. By running repeated engagement and disengagement cycles, friction wear rates for clutch facings can be determined.
Up next, ACT is designing a...
To read more, sign up for a digital subscription to PRI Magazine on Zinio here.
Once you download the Zinio mobile app or are logged into Zinio on a desktop browser, you will gain immediate access to more than a year's worth of content, including "Power Masters" here and more open wheel coverage in the May/June 2025 issue here.
Photo courtesy of The Driveshaft Shop